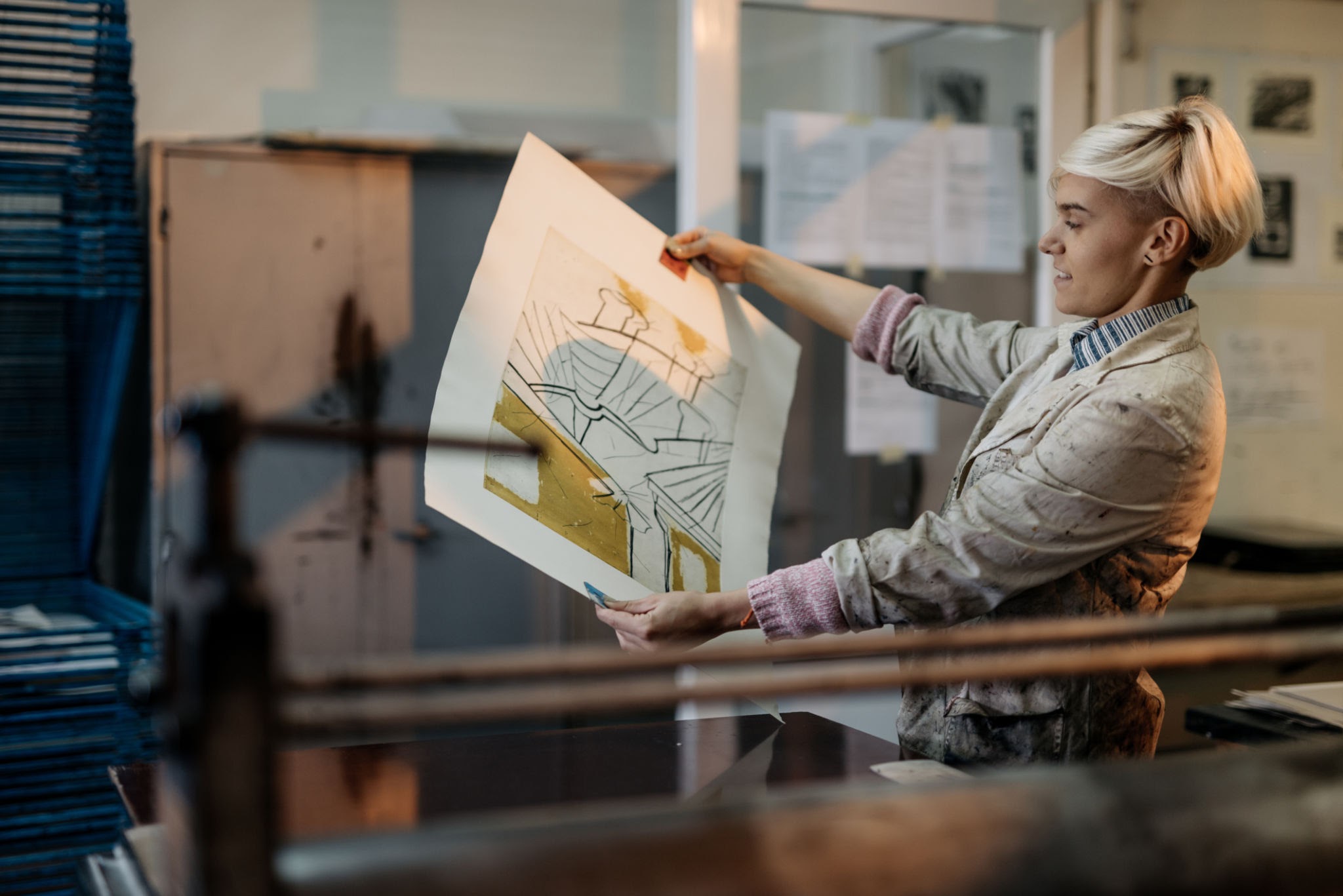
Innovative advances in photo etching are paving the way for a more sustainable manufacturing future. From closed-loop recycling systems that minimize chemical waste to the transition from mercury vapor lamps to energy-efficient LED units, eco-friendly photo etching technologies offer numerous benefits for both the environment and production efficiency.
The exploration of biodegradable photoresists further underscores the industry’s commitment to sustainability, while zero-discharge facilities serve as powerful proof points for what is possible with innovative water and chemical management solutions. Compliance with REACH and RoHS ensures that these advancements meet global standards, making them attractive not only from an environmental standpoint but also from a regulatory perspective.

Embracing these sustainable manufacturing practices can dramatically reduce the environmental footprint of photo etching, helping organizations achieve their green objectives and set new industry benchmarks for eco-friendly production. For ongoing updates and best practices in sustainable manufacturing, resources from EPA and the European Chemicals Agency are invaluable tools for further exploration.
Reducing Chemical Waste with Closed-Loop Systems
A major environmental challenge in photo etching is the management of chemical waste. Traditional systems often result in excessive disposal of etchants, which can be harmful to the environment. Recent breakthroughs in closed-loop systems are dramatically changing this scenario:
- Etchant Recycling Technologies:
Cutting-edge methods now allow for the regeneration of copper chloride and other etchants. By continuously recycling these chemicals, manufacturers can reduce waste and lower operating costs, while also adhering to environmental best practices. - Benefits of Closed-Loop Systems:
- Minimized chemical discharge into waterways.
- Extended etchant life, enhancing resource efficiency.
- Regulatory compliance with environmental standards such as REACH and RoHS.
For further reading on sustainable chemical recycling, the Environmental Protection Agency offers detailed insights into industry best practices.
Energy Efficiency in UV Exposure Units
Energy consumption is a critical concern in manufacturing. Advances in UV exposure units have shifted the balance toward more sustainable practices through innovative lighting solutions.
- LED vs. Mercury Vapor Lamps:
The transition from mercury vapor lamps to LED UV exposure units has resulted in a dramatic 40% reduction in energy consumption. This shift not only lowers energy bills but also minimizes harmful emissions associated with mercury use.
Below is a comparative table highlighting key differences:
Lighting Technology | Energy Consumption | Environmental Impact |
---|---|---|
Mercury Vapor Lamps | Higher energy usage | Potential mercury hazards |
LED UV Exposure Units | 40% lower energy consumption | Lower emissions and safer disposal |
Table: Comparison of energy efficiency and environmental impact between traditional mercury vapor lamps and modern LED UV exposure units.
This transition is critical for manufacturers seeking to reduce their environmental footprint, aligning with global sustainability goals.
Biodegradable Photoresists: Fact or Fiction?
The materials used in photo etching are also under scrutiny for their environmental impact. One area of emerging interest is the development of biodegradable photoresists.
- Soy-Based Resists:
Researchers and industry pioneers are exploring soy-based resists as a renewable alternative to conventional photoresists. Preliminary studies suggest that these resists can deliver comparable performance while being significantly more eco-friendly. - Compostable Masking Films:
Similarly, compostable masking films are being developed to replace traditional non-degradable materials. Although still in the nascent stages of market adoption, these innovations promise a reduction in landfill waste and a more sustainable lifecycle for etching processes.
These developments are exciting, yet they prompt the question: Are biodegradable photoresists a viable long-term solution? Continuous research and pilot programs are essential to confirm their effectiveness and scalability.
Case Study: Zero-Discharge Etching Facilities
Innovative implementations of sustainable photo etching are already making a tangible impact. A notable case study involves a German supplier who established a zero-discharge etching facility. Here are the key achievements of the facility:
- 95% Water Reuse:
By integrating advanced water treatment and recycling systems, the facility achieved an impressive 95% water reuse rate. This not only drastically cuts water consumption but also minimizes the environmental impact of the etching process. - Zero Chemical Discharge:
The closed-loop operation effectively eliminates the discharge of hazardous chemicals, ensuring compliance with strict environmental regulations and setting a benchmark for sustainable manufacturing.
For more details on pioneering sustainable manufacturing practices in Europe, the European Chemicals Agency is an excellent resource.
Certifications & Compliance (REACH, RoHS)
Adhering to environmental regulations is critical for companies operating in global markets. The integration of sustainable practices in photo etching must align with key certifications and regulations:
- REACH Compliance:
Manufacturers must ensure that all chemical substances used in the photo etching process comply with the European Union’s REACH regulation, which aims to protect human health and the environment from the risks posed by chemicals. - RoHS Certification:
The Restriction of Hazardous Substances (RoHS) directive further mandates limitations on specific hazardous materials. Meeting these standards is crucial for suppliers operating in defense, medical, and consumer electronics sectors. - Navigating Global Supply Chains:
A comprehensive understanding of these certifications ensures that sustainable manufacturing practices are not only environmentally beneficial but also commercially viable. Suppliers that meet these standards gain a competitive edge in global markets.
Environmental officers and sustainability advocates should closely monitor these regulations to drive continuous improvements in eco-friendly manufacturing technologies.